一、電木注塑工藝要點(diǎn)概述。
a、電木粉在預(yù)熱后的料筒種為粘度 低的熔料狀態(tài)
b、因電木粉中含有40%的填料,注塑阻力很大,故應(yīng)施加較大的注塑壓力
c、預(yù)塑前無(wú)需且不能對(duì)電木粉進(jìn)行烘干
d、注塑過(guò)程中因?yàn)殡娔镜墓袒^(guò)程伴隨著水汽和化學(xué)氣體的產(chǎn)生,模具應(yīng)開設(shè)排氣槽,甚至應(yīng)增加開模排氣工序。
e、塑化條件:背壓,螺桿轉(zhuǎn)速,料溫
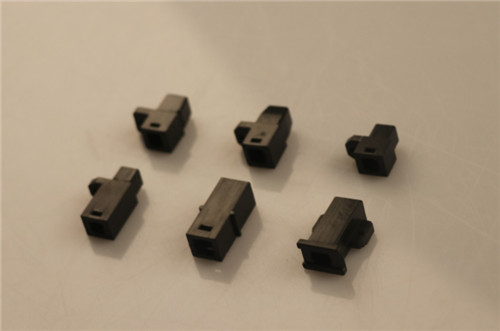
3、螺桿轉(zhuǎn)速越大,塑化時(shí)間越短,熔料無(wú)法充分塑化;螺桿轉(zhuǎn)速越小,塑化時(shí)摩擦越厲害,使得熔料溫度過(guò)高而提前固化,產(chǎn)生氣體,影響充型還會(huì)對(duì)螺桿料筒造成腐蝕,磨損加劇。
4、料溫過(guò)高,熔料在螺桿的剪切下迅速固化,使螺桿料筒磨損加劇,更無(wú)法注射,堵塞射咀;料溫過(guò)低,熔料塑化不充分,注射緩慢,無(wú)法充滿型腔,熔接痕明顯。一般,料溫應(yīng)控制在70~90℃之間,如原料PF-161J料溫應(yīng)在72~78℃為宜。
二、充模條件:射膠速度,射膠壓力,保壓時(shí)間
1、射膠速度太快,熔料與模具產(chǎn)生的摩擦熱越大,使熔料局部過(guò)早固化,甚至燒焦,同時(shí)固化產(chǎn)生的水汽和氣體無(wú)法排干凈,產(chǎn)生粉刺狀氣孔或者缺膠;射膠速度太忙,容易產(chǎn)生流痕和熔接痕。
2、射膠壓力太大,使熔膠塑型良好,機(jī)械性能良好,但增加了塑件的內(nèi)應(yīng)力,使毛邊變厚變大(毛邊以能被日光穿透為宜);射膠壓力太小,制品容易缺膠,多次缺膠容易導(dǎo)致模具粘料發(fā)黑,使產(chǎn)品表面失去光澤發(fā)白。
3、保壓時(shí)間越長(zhǎng),塑件的重量越大,塑件越密實(shí),但保壓時(shí)間太長(zhǎng)會(huì)造成脫模困難,保壓時(shí)間超過(guò)25秒后,塑件重量將不再增加;保壓時(shí)間越短,收縮率增加,保壓時(shí)間過(guò)短時(shí),生產(chǎn)周期變短,過(guò)早脫模將造成粘模和變形。
三、固化成型條件:模具溫度,冷卻時(shí)間
1、模具溫度越高,模具成型周期越短,提高了生產(chǎn)效率,但模溫過(guò)高時(shí),電木粉容易燒焦,出現(xiàn)針孔,還使得充入的熔料快速固化而來(lái)不及將產(chǎn)生的氣體完全排出而造成困氣,燒黃模具,產(chǎn)生粘模,發(fā)白等缺陷;模溫過(guò)低,熔膠前鋒流動(dòng)性變差,無(wú)法充滿型芯,更使得熔料固化結(jié)合不緊密,機(jī)械強(qiáng)度差,光澤度差。若冷卻時(shí)間不變,脫模時(shí)容易粘?;虍a(chǎn)生氣泡。
2、冷卻時(shí)間,模具溫度高,冷卻時(shí)間可在保證塑件尺寸在公差范圍內(nèi)的條件下適當(dāng)減少;塑件壁厚越大,冷卻時(shí)間就要相應(yīng)的增加。
脫模后退火處理:自然冷卻